DSEAR Regulations: All You Need to Know
Wednesday 14 June
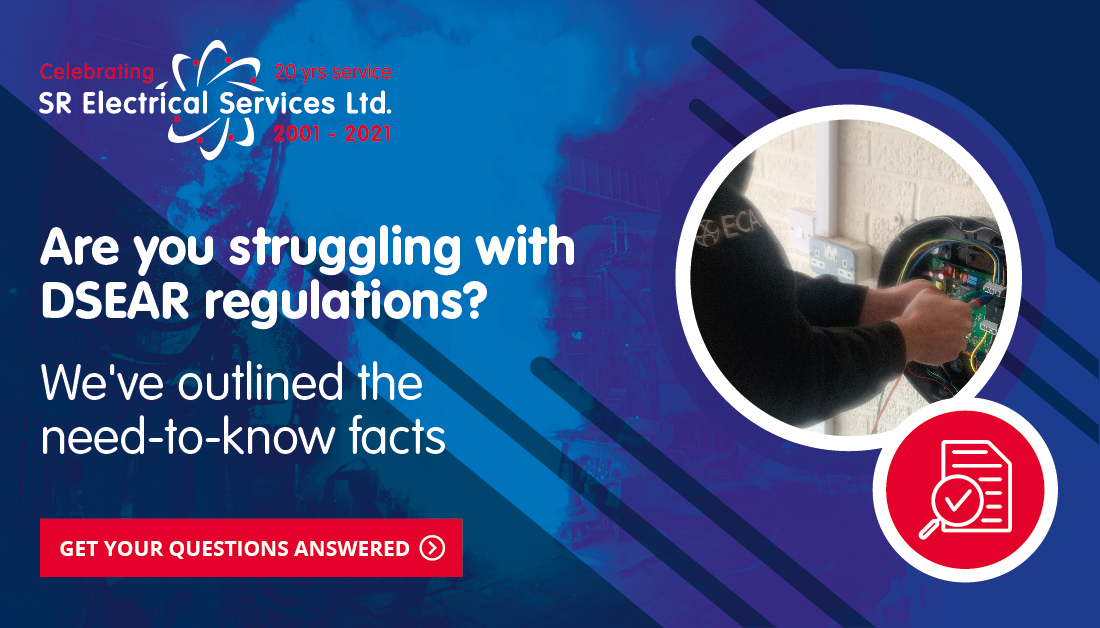
DSEAR requirements affect a huge variety of businesses sector-wide, particularly those with hazardous areas, and are ultimately in place to protect employees and members of the public. Although their purpose is straightforward, some aspects of DSEAR such as which substances are covered, can be confusing.
Luckily, we’re here to break down DSEAR regulations and offer you advice on how to keep your workplace compliant.
What exactly is DSEAR?
DSEAR is the abbreviation for the Dangerous Substances and Explosive Atmospheres Regulations 2002. The regulations feature a set of requirements for business owners to reduce the risks of harm to people that could result from dangerous substances.
One of the biggest questions surrounding DSEAR is, are they a legal requirement? And the answer is yes, businesses have a legal obligation to assess and control risks in their workplace.
What is considered a dangerous substance?
Simply put, dangerous substances cover any substances or mixtures of substances which could cause danger in the form of fires, thermal runaway or metal corrosion. This includes:
- Flammable gases (such as LPG)
- Pressurised gases
- Solvents
- Paints
- Dusts (from machining, sanding and food production)
- Substances corrosive to metal
If a substance in your workplace has physical properties such as a high flash point, that could lead to a fire or explosion, then this must be covered by DSEAR regulations.
Which industries fall under DSEAR?
As previously mentioned, DSEAR regulations affect many businesses due to the wide amount of substances that can potentially cause fire or explosions. In our experience, the most prevalent industries are:
- Petrochemical sites
- Businesses that store fuel
- Manufacturers that handle waste dusts
- Laboratories that use flammable solvents
- Retailers who stock flammable goods
How do I comply with DSEAR?
There are 6 key measures you must put in place to reduce the risks concerned with DSEAR:
1. Assess the risks
You must assess the risks of the dangerous substances that surround your work. This includes the examination of the dangerous substances present, the activities surrounding them and how these factors can cause potential harm.
2. Prevent or control known risks
Once risks are identified, measures have to be put in place to either completely eliminate the risks or lessen them as much as possible. In some cases, this can mean swapping out substances or finding new working methods (substitution).
3. Put control measures in place
If there is no way of eliminating the identified dangerous substance, the next best thing is to put control measures in place. For example, avoiding ignition sources and controlling the release of dangerous substances.
4. Have a plan set
In the unfortunate event of an emergency, plans and procedures must be in place which include:
- Safety drills
- Communication and warning systems
- Equipment for repair workers
These measures must be proportionate to the risk and these emergency plans must be made available to the emergency services.
5. Keep employees informed
DSEAR regulations are in place to protect employees, and so they must be kept informed with the appropriate information and training. Employees need to be told about the dangerous substances present and their risks, assessment findings, control measures and emergency procedures.
6. Identify areas of risk
This measure pertains particularly to explosive atmospheres, and if they are present at your property, then they must be identified and correctly classified to reduce the dangers surrounding ignition sources.
We have previously shared a helpful guide on classifying ATEX areas, read further in-depth here.
How can I get a DSEAR assessment?
It’s noted that a DSEAR assessment must be completed by a ‘competent person’, and though there are no solid qualifiers for this definition, the individual must have detailed knowledge of the regulations and the experience to support this.
Due to the nature of DSEAR and the risks surrounding dangerous substances, it is always a good idea to rely on the advice of a professional.
The next steps
Here at SR Electrical Services, we can take the stress of getting your head around this legislation away! We carry out in-depth inspections and assessments of your workplace to ensure that they comply with DSEAR regulations.
Our team are experts in hazardous areas with accreditations from CompEx, ECA and NICEIC. If you require advice on the mentioned regulations, then don’t hesitate to get in touch with us here.
Latest News
View all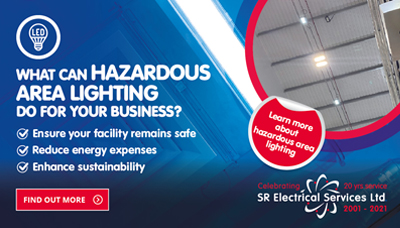
Your Quick Guide To Hazardous Area Lighting
Good lighting is crucial in keeping your facility well-lit and safe, however electrical ignition sources are one of the most common causes of fire and explosion in hazardous areas.
Read more about Your Quick Guide To Hazardous Area Lighting
Share
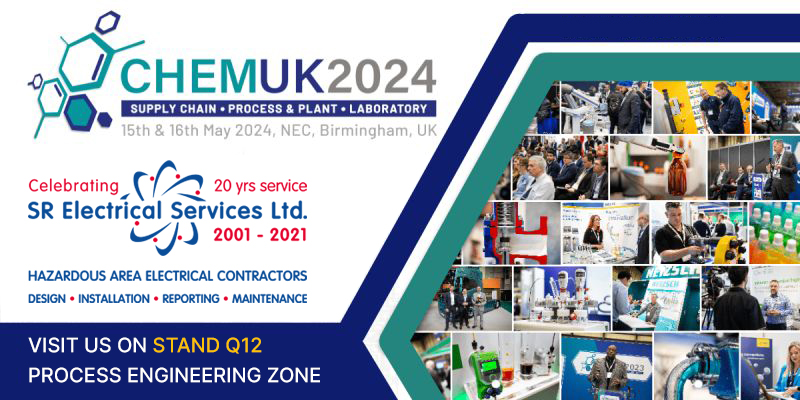
SR Electrical Will Be At CHEMUK 2024 This May!
We are excited to announce that SR Electrical will be at CHEMUK 2024 this Spring! The Chemical UK expo is the UK’s largest annual trade show for the chemical, laboratory and process industry.
Read more about SR Electrical Will Be At CHEMUK 2024 This May!
Share
Latest Projects
View all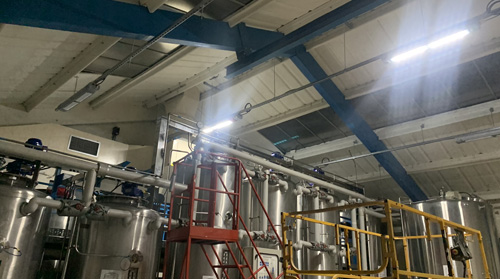
ATEX Certified Hazardous Area Lighting and Emergency Lighting
Our team helped a business in the food industry improve the lighting in their hazardous areas with the supply and installation of fully compliant, ATEX certified fittings.
Read more about ATEX Certified Hazardous Area Lighting and Emergency Lighting
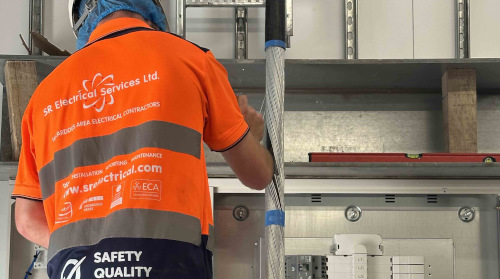
ATEX Lighting & Electrics Installation
Recently, we were called in to help a business in the food manufacturing sector with new hazardous area electrics at their site.
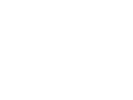
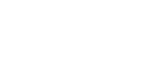
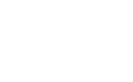
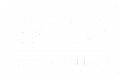

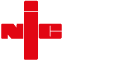
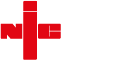
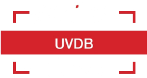
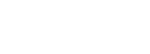